Exploring GRP Composite Housings: Benefits and Applications
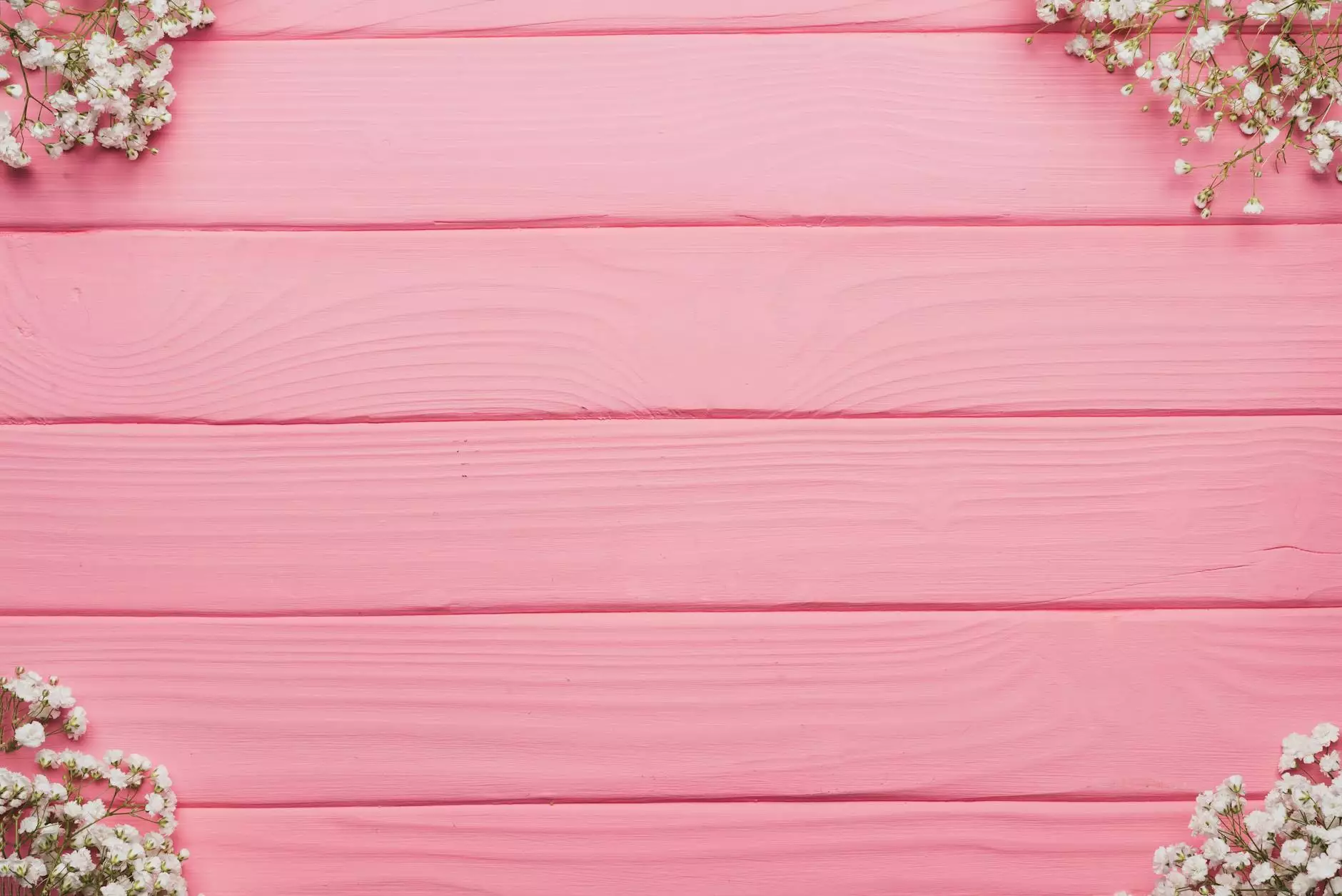
GRP composite housings, or Glass Reinforced Plastic composite housings, are making significant waves across multiple industries due to their impressive properties and numerous applications. This comprehensive article will delve into what GRP composite housings are, explore their benefits, and illustrate their varied applications, making a compelling case for their use in modern engineering and manufacturing.
Understanding GRP Composite Housings
GRP composite housings are engineered from a combination of glass fibers and resins, providing a material that is both lightweight and exceptionally strong. The incorporation of glass fibers enhances the composite's mechanical properties, giving it a rigidity that outperforms many metals and plastics while keeping the weight down.
What Makes GRP Composite Housings Unique?
The uniqueness of GRP composite housings lies in their balance of strength, weight, and corrosion resistance. Typical materials like steel or aluminum can be heavy and susceptible to corrosion, while plastics may lack the necessary strength for certain applications. GRP composites step in as a versatile alternative.
- Lightweight: They weigh a fraction of what metals do, reducing transportation costs and facilitating easier handling.
- Corrosion Resistance: GRP composites are immune to rust and corrosion, making them ideal for harsh environments.
- Durability: Withstanding environmental stressors, GRP maintains its integrity over time.
- Thermal Insulation: They provide excellent thermal insulation properties, enhancing energy efficiency.
Benefits of Using GRP Composite Housings
Implementing GRP composite housings comes with a plethora of benefits, making them an attractive option for engineers and manufacturers:
1. Cost Efficiency
While the initial costs can be slightly higher than traditional materials, the longevity and durability of GRP composites lead to long-term savings. Their resistance to wear and tear means fewer replacements and maintenance costs in the long run.
2. Environmental Impact
As sustainability becomes more critical, GRP composite housings offer an eco-friendlier option. Their longevity reduces waste, and many manufacturers are now moving towards the use of recyclable resins.
3. Design Flexibility
Engineers appreciate the design flexibility that comes with using composite materials. GRP can be molded into complex shapes that would be challenging or impossible to achieve with traditional metals, allowing for innovative solutions that enhance product performance.
4. Enhanced Safety Features
In many applications, especially in electrical and mechanical fields, GRP composite housings provide safety from electrical conductivity. This insulating property makes them a preferred choice for enclosures around sensitive equipment.
Applications of GRP Composite Housings
The applications for GRP composite housings span numerous industries. Here are some of the most significant areas where they are used:
1. Electrical and Electronics Enclosures
In the electrical industry, the ability of GRP to act as an insulator is invaluable. GRP composite housings are extensively used for switches, transformers, and electronic communication boxes, ensuring safety and durability in challenging environments.
2. Marine Industry
The harsh marine environment poses significant challenges for traditional materials. GRP composites, with their resistance to corrosion, are ideal for boat hulls, decks, and underwater components, greatly extending the lifespan of marine equipment.
3. Aerospace and Automotive Applications
The aerospace and automotive sectors benefit from the lightweight and strong properties of GRP composite housings. Components like panels, casings, and frames can be made lighter, improving fuel efficiency and performance without compromising safety.
4. Construction Industry
In construction, GRP can be found in structural applications including staircases, cladding, and roofing materials. Its resistance to physical stress and temperature fluctuations ensures a sustainable choice for building materials.
5. Telecommunications
The telecommunications industry also relies heavily on GRP composites to protect sensitive electronic housing against environmental hazards. The robust nature of GRP composite housings ensures connectivity and reliability even under adverse conditions.
Innovative Manufacturing Processes for GRP Composite Housings
The production of GRP composite housings has evolved significantly from traditional methods. Today, advanced techniques such as:
- Hand Layup: A manual process where glass fibers are layered and resin is applied. This method allows for customization but can be labor-intensive.
- Spray-Up: In this method, glass fibers are sprayed with resin, allowing for faster production times while maintaining quality.
- Automated Fiber Placement: A highly efficient technique that uses robotics to precisely place fibers, offering consistent quality and reducing waste.
Challenges and Considerations in GRP Composite Housing Usage
While there are numerous advantages to using GRP composite housings, it is essential to consider potential challenges:
1. Initial Costs
The initial investment for GRP composites can be higher than traditional materials. However, considering the lifecycle costs, they often prove to be more economical in the long run.
2. UV Degradation
When exposed to sunlight, GRP can degrade unless properly treated. Coatings or UV-resistant materials may be required for outdoor applications.
3. Limited High-Temperature Resistance
While GRP can handle a wide range of temperatures, there are limitations. It's crucial to assess the temperature requirements of the application to select the appropriate resin type.
The Future of GRP Composite Housings
The future of GRP composite housings looks promising, with continuous innovations on the horizon. Advances in resin chemistry and fiber technology are leading to even better performance, making these materials suitable for an even broader range of applications.
1. Bio-based Resins
With an increasing emphasis on sustainability, manufacturers are exploring bio-based resin alternatives that can further reduce the environmental impact of GRP composite housings.
2. Smart Composites
Integration of sensors within GRP composites is another innovative direction, allowing for real-time monitoring of structural integrity and ensuring safety and reliability in critical applications.
Conclusion
In conclusion, GRP composite housings offer a multitude of advantages across various industries, showcasing their superior strength, light weight, and versatility. As technology continues to advance, the applications of GRP composites will undoubtedly expand, making them a vital component in modern manufacturing and engineering. Their capacity to provide cost-effective, sustainable, and safe solutions affirms their position as a material of choice in numerous applications.
For more information on GRP composite housings and how they can benefit your specific needs, visit Celtic Composites.