Understanding Injection Mold Tooling: A Deep Dive into Its Significance and Benefits
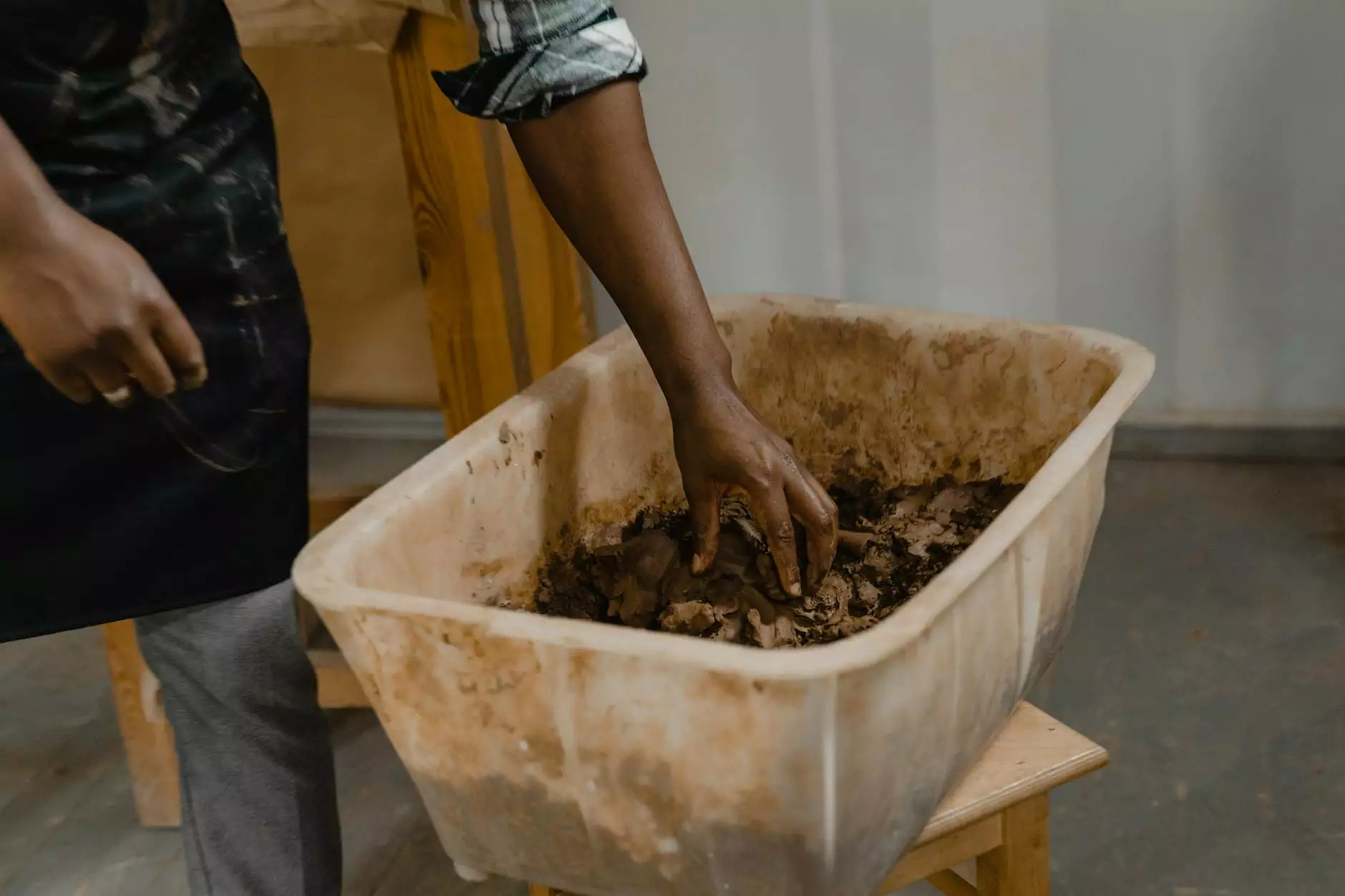
The field of manufacturing has evolved significantly over the years, and one of the most innovative processes that has transformed production efficiency and quality is injection mold tooling. This method is not only crucial for creating precise parts at high volumes but also influences the economics of production in various industries. In this article, we will explore the concept of injection mold tooling, its applications, benefits, and why it is a cornerstone for manufacturers, particularly in sectors such as automotive, aerospace, and consumer products.
What is Injection Mold Tooling?
Injection mold tooling involves creating a hollow plastic part by injecting molten material into a mold. The process begins with the design of the mold and then transitions into the production phase where the actual molding occurs.
Components of Injection Mold Tooling
The injection mold tooling process comprises several key components:
- Mold Design: The design phase is critical as it directly affects the quality of the final product.
- Mold Materials: Commonly used materials for mold-making include steel and aluminum, chosen based on durability and cost.
- Injection Molding Machine: This equipment melts and injects plastic into the mold cavity.
- Cooling System: Effective cooling ensures optimal cycle times and enhances production efficiency.
The Process of Injection Molding
The injection mold tooling process can be broken down into several distinct phases:
1. Mold Design and Prototyping
The journey begins with an ideation phase where engineers collaborate to develop mold designs. Using software like CAD, intricate designs are created and tested in virtual simulations to validate functionality.
2. Material Selection
Material selection is pivotal. Most commonly, thermoplastics such as ABS, polycarbonate, and nylon are used due to their excellent moldability and physical properties.
3. Injection Molding
Here, the selected material is heated until it reaches a molten state and injected under pressure into the mold. This pressure ensures that every detail is captured. Once injected, the material cools and solidifies into the desired shape.
4. Ejection
After the part has cooled, ejector pins in the mold push out the finished product, ready for inspection and packaging.
Applications of Injection Mold Tooling
Injection mold tooling finds applications across various industries, such as:
- Automotive: Used for making interior and exterior components.
- Aerospace: Critical for creating lightweight and precision parts.
- Consumer Products: From plastic containers to toys, this process is integral to making everyday items.
- Medical Devices: Ensures the production of reliable and sterile components.
Benefits of Injection Mold Tooling
The use of injection mold tooling provides several benefits, making it a preferred choice for manufacturers:
1. High Production Efficiency
Once the mold is created, producing parts is fast and efficient, reducing lead times significantly.
2. Cost-Effectiveness
High-volume production leads to lower costs per unit, making it economically viable for mass production.
3. Design Flexibility
Design changes can be implemented without extensive modifications in tooling, allowing for rapid prototyping and adaptation.
4. Quality Consistency
Injection molding ensures high precision and repeatability of manufactured parts, leading to consistent quality across production runs.
Challenges in Injection Mold Tooling
Despite its numerous benefits, injection mold tooling does come with challenges:
- High Initial Costs: The upfront costs for mold creation can be significant, though this is offset by long-term production savings.
- Complex Design Limitations: Highly complex designs may require intricate mold designs, increasing time and cost.
- Material Constraints: Not all materials are suitable for injection molding, which can limit design options.
The Future of Injection Mold Tooling
As technology advances, injection mold tooling continues to evolve. Key trends shaping its future include:
1. Automation and Smart Manufacturing
Integrating automation in the manufacturing process can improve efficiency and reduce human error.
2. Sustainable Materials
With an increasing focus on sustainability, the development of biodegradable plastics and recyclable materials will likely gain momentum.
3. Advanced Simulation Technologies
Utilizing advanced simulation tools for mold design and injection processes enhances accuracy and speeds up development.
Conclusion
In conclusion, injection mold tooling is an essential technique in modern manufacturing that has transformed how products are produced. Its efficiency, cost-effectiveness, and ability to maintain high quality make it indispensable across various industries. Continued advancements in technology will further enhance its capabilities, ensuring that it remains at the forefront of manufacturing innovation.
For businesses looking to leverage the advantages of injection mold tooling, partnering with proficient manufacturers like DeepMould can provide the expertise and quality needed to excel in the competitive market of metal fabricators.